Scanning electron microscope was used to observe the fatigue fracture and analyze the fracture mechanism; at the same time, spin bending fatigue test was carried out on the decarburized specimens at different temperatures to compare the fatigue life of the test steel with and without decarburization, and to analyze the effect of decarburization on the fatigue performance of the test steel. The results show that, due to the simultaneous existence of oxidation and decarburization in the heating process, the interaction between the two, resulting in the thickness of the fully decarburized layer with the growth of the temperature shows a trend of increasing and then decreasing, the thickness of the fully decarburized layer reaches a maximum value of 120 μm at 750 ℃, and the thickness of the fully decarburized layer reaches a minimum value of 20 μm at 850 ℃, and the fatigue limit of the test steel is about 760 MPa, and the source of fatigue cracks in the test steel is mainly Al2O3 non-metallic inclusions; decarburization behavior greatly reduces the fatigue life of the test steel, affecting the fatigue performance of the test steel, the thicker the decarburization layer, the lower the fatigue life. In order to reduce the impact of decarburization layer on the fatigue performance of the test steel, the optimal heat treatment temperature of the test steel should be set at 850℃.
Gear is an important component of automobile,due to the operation at high speed, the meshing part of the gear surface must have high strength and abrasion resistance, and the tooth root must have good bending fatigue performance due to the constant repeated load, in order to avoid cracks that lead to material fracture. Research shows that decarburization is an important factor affecting the spin bending fatigue performance of metal materials, and spin bending fatigue performance is an important indicator of product quality, so it is necessary to study the decarburization behavior and spin bending fatigue performance of the test material.
In this paper, the heat treatment furnace on the 20CrMnTi gear steel surface decarburization test, analyze different heating temperatures on the test steel decarburization layer depth of the changing law; using QBWP-6000J simple beam fatigue testing machine on the test steel rotary bending fatigue test, determination of test steel fatigue performance, and at the same time to analyze the impact of decarburization on the fatigue performance of the test steel for the actual production to improve the production process, enhance the quality of products and provide a reasonable reference. The test steel fatigue performance is determined by the spin bending fatigue test machine.
1. Test materials and methods
Test material for a unit to provide 20CrMnTi gear steel, the main chemical composition as shown in Table 1. Decarburization test: the test material is processed into Ф8 mm × 12 mm cylindrical specimen, the surface should be bright without stains. Heat treatment furnace were heated to 675 ℃, 700 ℃, 725 ℃, 750 ℃, 800 ℃, 850 ℃, 900 ℃, 950 ℃, 1,000 ℃, into the specimen and hold 1 h, and then air-cooled to room temperature. After heat treatment of the specimen by setting, grinding and polishing, with 4% of the nitric acid alcohol solution erosion, the use of metallurgical microscopy to observe the test steel decarburization layer, measuring the depth of decarburization layer at different temperatures. Spin bending fatigue test: the test material according to the requirements of the processing of two groups of spin bending fatigue specimens, the first group does not carry out decarburization test, the second group of decarburization test at different temperatures. Using the spin bending fatigue testing machine, the two groups of test steel for spin bending fatigue testing, determination of the fatigue limit of the two groups of test steel, comparison of the fatigue life of the two groups of test steel, the use of scanning electron microscope fatigue fracture observation, analyze the reasons for the fracture of the specimen, to explore the effect of decarburization of the fatigue properties of the test steel.
Table 1 Chemical composition (mass fraction) of test steel wt%
Effect of heating temperature on decarburization
The morphology of decarburization organization under different heating temperatures is shown in Fig. 1. As can be seen from the figure, when the temperature is 675 ℃, the sample surface does not appear decarburization layer; when the temperature rises to 700 ℃, the sample surface decarburization layer began to appear, for the thin ferrite decarburization layer; with the temperature rises to 725 ℃, the sample surface decarburization layer thickness increased significantly; 750 ℃ decarburization layer thickness reaches its maximum value, at this time, the ferrite grain is more clear, coarse; when the temperature rises to 800 ℃, the decarburization layer thickness began to decrease significantly, its thickness fell to half of the 750 ℃; when the temperature continues to rise to 850 ℃ and the thickness of decarburization is shown in Fig. 1. 800 ℃, the full decarburization layer thickness began to decrease significantly, its thickness fell to 750 ℃ when half; when the temperature continues to rise to 850 ℃ and above, the test steel full decarburization layer thickness continues to decrease, half decarburization layer thickness began to gradually increase until the full decarburization layer morphology all disappeared, half decarburization layer morphology gradually clear. It can be seen that the thickness of the fully decarburized layer with the increase in temperature was first increased and then reduced, the reason for this phenomenon is due to the sample in the heating process at the same time the oxidation and decarburization behavior, only when the decarburization rate is faster than the speed of oxidation will appear decarburization phenomenon. At the beginning of heating, the thickness of the fully decarburized layer increases gradually with the increase in temperature until the thickness of the fully decarburized layer reaches the maximum value, at this time to continue to raise the temperature, the specimen oxidation rate is faster than the decarburization rate, which inhibits the increase of the fully decarburized layer, resulting in a downward trend. It can be seen that, within the range of 675 ~950 ℃, the value of the thickness of the fully decarburized layer at 750 ℃ is the largest, and the value of the thickness of the fully decarburized layer at 850 ℃ is the smallest, therefore, the heating temperature of the test steel is recommended to be 850℃.
Fig.1 Histomorphology of decarburized layer of test steel held at different heating temperatures for 1h
Compared with the semi-decarburized layer, the thickness of the fully decarburized layer has a more serious negative impact on the material properties, it will greatly reduce the mechanical properties of the material, such as reducing the strength, hardness, wear resistance and fatigue limit, etc., and also increase the sensitivity to cracks, affecting the quality of welding and so on. Therefore, controlling the thickness of the fully decarburized layer is of great significance to improve product performance. Figure 2 shows the variation curve of the thickness of the fully decarburized layer with temperature, which shows the variation of the thickness of the fully decarburized layer more clearly. It can be seen from the figure that the thickness of the fully decarburized layer is only about 34μm at 700℃; with the temperature rising to 725 ℃, the thickness of the fully decarburized layer increases significantly to 86 μm, which is more than two times of the thickness of the fully decarburized layer at 700 ℃; when the temperature is raised to 750 ℃, the thickness of the fully decarburized layer When the temperature rises to 750℃, the thickness of the fully decarburized layer reaches the maximum value of 120 μm; as the temperature continues to rise, the thickness of the fully decarburized layer starts to decrease sharply, to 70 μm at 800℃, and then to the minimum value of about 20μm at 850℃.
Fig.2 Thickness of fully decarburized layer at different temperatures
Effect of decarburization on fatigue performance in spin bending
In order to study the effect of decarburization on the fatigue properties of spring steel, two groups of spin bending fatigue tests were carried out, the first group was fatigue testing directly without decarburization, and the second group was fatigue testing after decarburization at the same stress level (810 MPa), and the decarburization process was held at 700-850 ℃ for 1 h. The first group of specimens is shown in Table 2, which is the fatigue life of the spring steel.
The fatigue life of the first group of specimens is shown in Table 2. As can be seen from Table 2, without decarburization, the test steel was only subjected to 107 cycles at 810 MPa, and no fracture occurred; when the stress level exceeded 830 MPa, some of the specimens began to fracture; when the stress level exceeded 850 MPa, the fatigue specimens were all fractured.
Table 2 Fatigue life under different stress levels (without decarburization)
In order to determine the fatigue limit, the group method is used to determine the fatigue limit of the test steel, and after statistical analysis of the data, the fatigue limit of the test steel is about 760 MPa; in order to characterize the fatigue life of the test steel under different stresses, the S-N curve is plotted, as shown in Figure 3. As can be seen from Figure 3, different stress levels correspond to different fatigue life, when the fatigue life of 7, corresponding to the number of cycles for 107, which means that the specimen under these conditions are through the state, the corresponding stress value can be approximated as the fatigue strength value, that is, 760 MPa. It can be seen that the S - N curve is important for the determination of the fatigue life of the material has an important reference value.
Figure 3 S-N curve of experimental steel rotary bending fatigue test
The fatigue life of the second group of specimens is shown in Table 3. As can be seen from Table 3, after the test steel is decarburized at different temperatures, the number of cycles is obviously reduced, and they are more than 107, and all the fatigue specimens are fractured, and the fatigue life is greatly reduced. Combined with the above decarburized layer thickness with the temperature change curve can be seen, 750 ℃ decarburized layer thickness is the largest, corresponding to the lowest value of fatigue life. 850 ℃ decarburized layer thickness is the smallest, corresponding to the fatigue life value is relatively high. It can be seen that the decarburization behavior greatly reduces the fatigue performance of the material, and the thicker the decarburized layer, the lower the fatigue life.
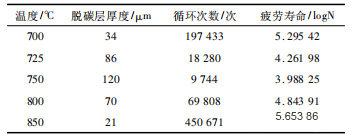
Table 3 Fatigue life at different decarburization temperatures (560 MPa)
The fatigue fracture morphology of the specimen was observed by scanning electron microscope, as shown in Fig. 4. Figure 4(a) for the crack source area, the figure can be seen obvious fatigue arc, according to the fatigue arc to find the source of fatigue, can be seen, the crack source for the "fish-eye" non-metallic inclusions, inclusions at the easy to cause stress concentration, resulting in fatigue cracks; Fig. 4(b) for the crack extension area morphology, can be seen obvious fatigue stripes, was river-like distribution, belongs to quasi-dissociative fracture, with cracks expanding, eventually leading to fracture. Figure 4(b) shows the morphology of crack expansion area, obvious fatigue streaks can be seen, in the form of river-like distribution, which belongs to quasi-dissociative fracture, and with the continuous expansion of the cracks, ultimately leading to fracture.
Fatigue fracture analysis
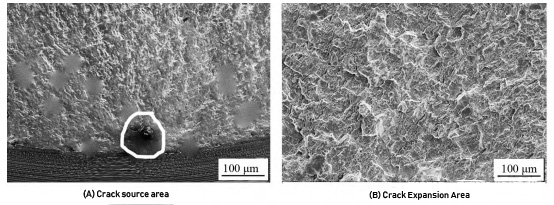
Fig.4 SEM morphology of fatigue fracture surface of experimental steel
In order to determine the type of inclusions in Fig. 4, energy spectrum composition analysis was carried out, and the results are shown in Fig. 5. It can be seen that the non-metallic inclusions are mainly Al2O3 inclusions, indicating that the inclusions are the main source of cracks caused by inclusions cracking.
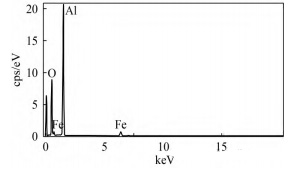
Figure 5 Energy Spectroscopy of Non-metallic Inclusions
Conclude
( 1) Positioning the heating temperature at 850 ℃ will minimize the thickness of the decarburized layer to reduce the effect on the fatigue performance.
( 2) The fatigue limit of the test steel spin bending is 760 MPa.
( 3) The test steel cracking in non-metallic inclusions, mainly Al2O3 mixture.
( 4) decarburization seriously reduce the fatigue life of the test steel, the thicker the decarburization layer, the lower the fatigue life.
Post time: Jun-21-2024